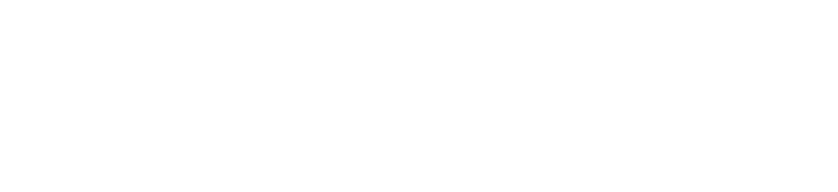
We've been walking for 60 years.
It was a very long and lonely road.
We've been walking for 60 years.
It was a very long and lonely road.
Youngdo, which supplies the world's highest quality velvet, has weaving and dyeing technology that no other competitor can imitate.
In particular, the technology that adds elasticity to the pile through special yarn processing before weaving and the technology of dyeing with time control are knowledge accumulated from long experience.
In addition, while competitors do not have their own dyeing and processing facilities and subcontract all processes to small businesses,
Youngdo owns state-of-the-art machinery and equipment introduced from advanced countries and produces products through strict management.
Youngdo has recorded 60 years of know-how to welcome the renaissance of velvet in the renaissance era by developing the global velvet industry.
Since all products of Youngdo Velvet use micro-fiber level, the strength and elongation of the yarn are increased through a twisting process that combines several strands of yarn and gives them a constant twist. It also provides Youngdo Velvet's unique touch and flexible silhouette.
This is the process of winding the thread to be used for the warp to the beam. Since all Youngdo Velvet products are woven with a dense and high density, the number of yarn strands in the warp beam should be about 100 or more per inch.
All products of Youngdo Velvet are woven with yarn thinner than a human hair. So, in order to improve weaving and reduce the defect rate, it goes through the process of applying glue (sizing agent) to the yarn. Youngdo Velvet's state-of-the-art sizing facilities and systematic technology not only prevent static electricity from occurring in the yarn, but also lay down fine hairs and prevent the yarn from breaking during weaving.
Youngdo Velvet not only values the pile quality of the outer surface, but also the quality of the ground, the bottom of the product. If you look at the background of all products produced by Youngdo Velvet, there are characteristics that differentiate them from other competitor products. The elasticity and touch of the fabric, and excellent drapability. One of the important processes essential to producing such high-quality velvet is to remove the oil contained in the yarn. This process not only softens the elasticity and feel of the thread, but also helps to maintain the permanent style that fashion products aim for.
Youngdo Velvet owns 182 rapier looms that can produce 8 million yards of velvet products annually. Based on the technology patented in 1981 for the manufacturing method of cut pile fabric (Patent No. 0009974), 22 German rapier looms were introduced in 1983 to produce cotton velvet, and in 1995, rapier with an automated system was established. Added 132 looms. Youngdo Velvet's rapier loom is capable of producing more than 20,000 ultra-high-density products per square centimeter on average with fine yarns such as microfiber. In particular, Youngdo Velvet's LCD rubbing cloth, which accounts for more than 90% of the global LCD rubbing cloth industry, developed an ultra-high density level of 90,000ea/㎠ in 2020 following the commercialization of 40,000ea/㎠ in 2010.
All Youngdo Velvet products have three eagle figures or three golden lines engraved in jacquard, which were applied for trademark in Selvage in 1973. It is the symbol of [Youngdo Three Eagle Mode] known in the world market. This method will increase the production cost, but it is to ensure that customers can verify that it is a Youngdo product and to fulfill the responsibility for the best quality, which is Youngdo's corporate spirit. This series of works is also an example of Youngdo Velvet's emotional management that loves customers.
The excellent luster and soft feel of velvet are determined by the pile processing technology applicable to the velvet surface. Youngdo Velvet's brushing process goes through a two-step continuous process that minimizes pile height variation and brushing angle variation for precise pile height control and excellent surface evenness. Although this series of processes adds 32 cents of weaving cost per yard, it gives high product value and supports high profit generation for Youngdo Velvet customers.
Youngdo Velvet has a batch process facility and key element technologies necessary for the pre-processing process (washing-scouring-reduction, etc.), dyeing process, and post-processing process in velvet dyeing on a site of about 13,000 square meters.
Youngdo Velvet has optimized dyeing technology to reproduce high-quality, beautiful color products and the only state-of-the-art facility for velvet dyeing processing in Korea. There is equipped with various dyeing facilities such as a tank dyeing machine for dyeing soft and fine acetate and rayon-based fibers, a CPB (Cold Pad Batch) dyeing machine for low-temperature aged dyeing such as cotton and Tencel, and a rapid dyeing machine exclusively for polymer materials for high-pressure dyeing at 180℃ or higher.
In line with recent eco-friendly trends, the dyeing process has also strengthened environmentally friendly dyeing methods and wastewater treatment facilities that minimize environmental pollution. As a result, it passed ISO 14001, an environmental management system, OEKO-TEX, an eco-friendly textile certification program, and GRS (Global Recycled Standard).
Youngdo Velvet has 3 state-of-the-art tenters. As the dyed velvet passes through a tenter, a high-temperature hot air machine with a height of more than 30m, it not only dries the product, but also adjusts the shape stability, tissue stabilization, and fabric width. In addition, anti-static processing and resin processing are also performed according to customer requests.
We will head for new experiences
while maintaining the pride of Velvet.
COPYRIGHT ⓒ 2022 YOUNGDO VELVET.
ALL RIGHTS RESERVED.
CONTACT US